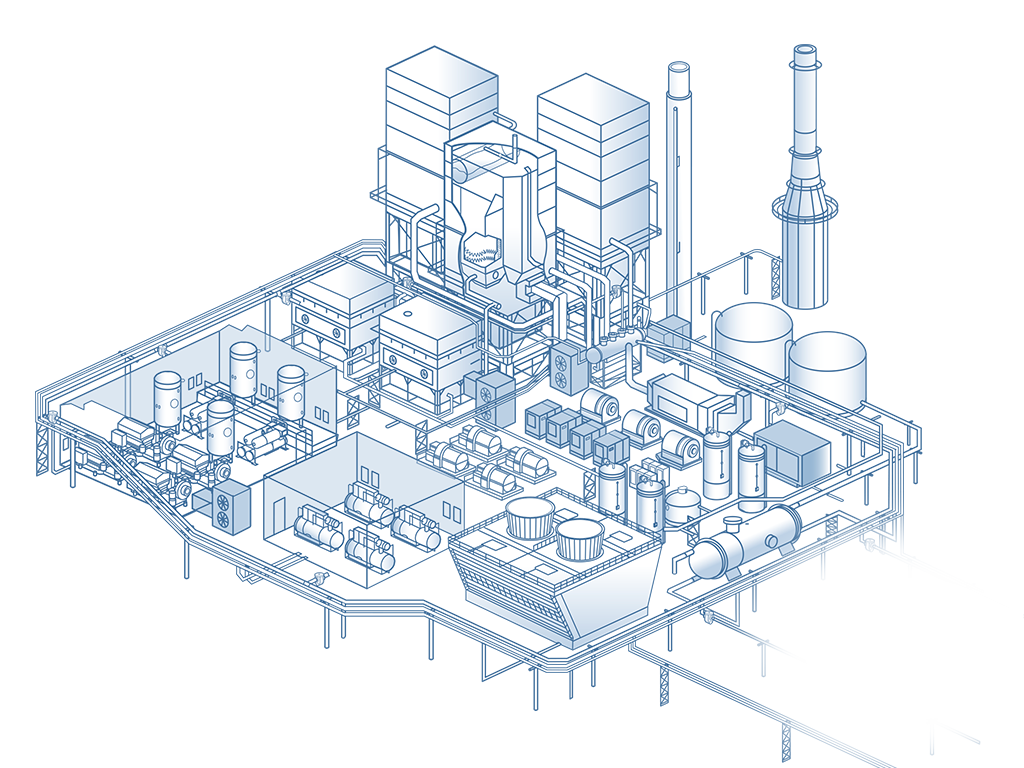
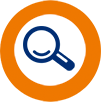
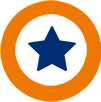
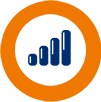
software/analytics that create
alerts and reports
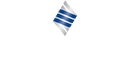
Emerson Energy Advisor
Energy Management
Information System (EMIS)
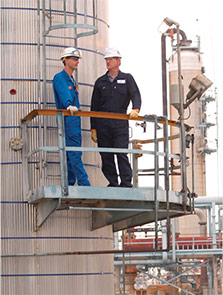
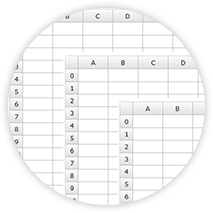
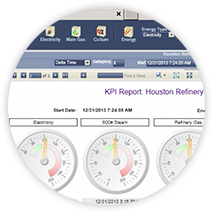
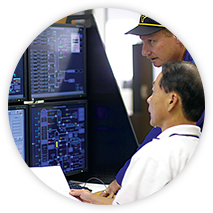
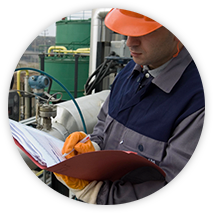
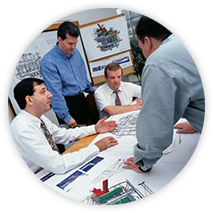
What is an Energy Management Information System?
- Collects measurements and helps you manage energy
- May be as simple as spreadsheets, or as powerful as a graphics-based system
- Provides fundamental information for decisions affecting your energy use
Why Do I Want An EMIS?
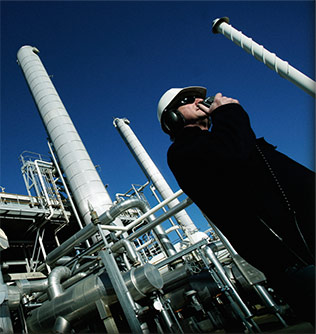
Reduce total energy costs by 5% - 10%
(or usually more)
- Gives you the information to make timely decisions about your organization's energy use
- Establish, track and maintain real and achievable targets for energy reduction
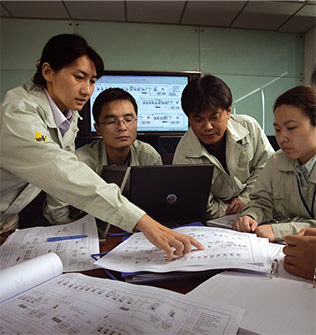
Create an "Energy Culture" within your organization
- Management
- Set/enforce energy goals as a critical priority
- Set key performance indicators (KPIs)
- Set budgets for energy reduction
- Prioritize energy projects
- Operations
- Establish accountability, contribution
- Operate to energy KPIs
- Know when your energy use is high, and why
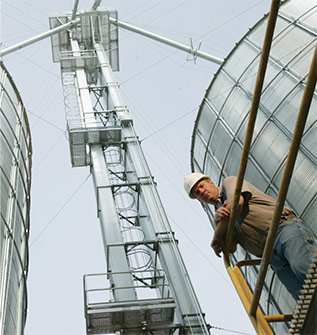
Establish a reputation for sustainability
- Implement a positive corporate social responsibility program for energy savings and emissions reduction
Why Do I Want An EMIS?
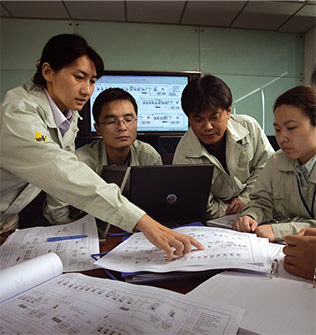
Create an "Energy Culture" within your organization
- Management
- Set/enforce energy goals as a critical priority
- Set Key Performance Indicators (KPI's)
- Set budgets for energy reduction
- Prioritize energy projects
- Operations
- Establish accountability, contribution
- Operate to energy KPI’s
- Know when your energy use is high, and why
Why Do I Want An EMIS?
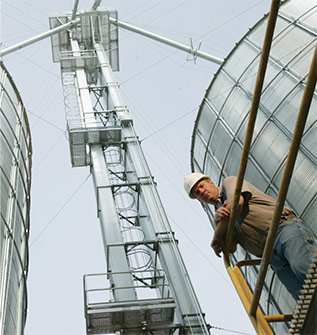
Establish a reputation for sustainability
- Implement a positive corporate social responsibility program for energy savings and emissions reduction
How Does It Work?


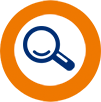
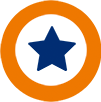
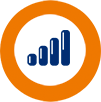
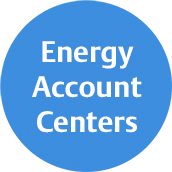

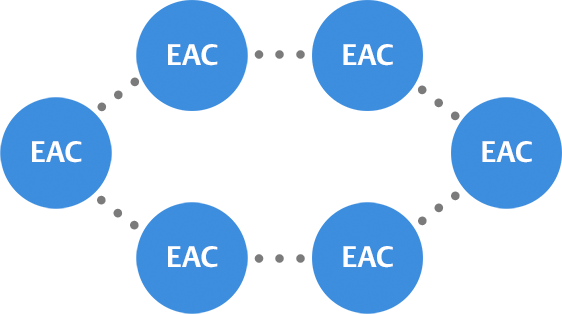
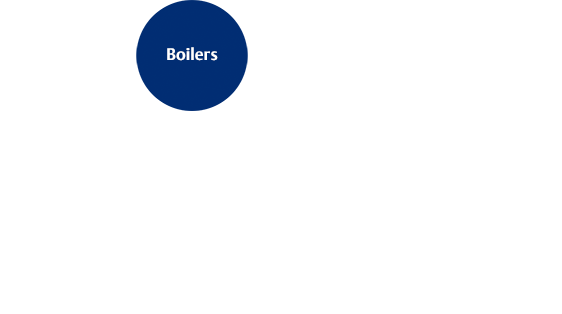
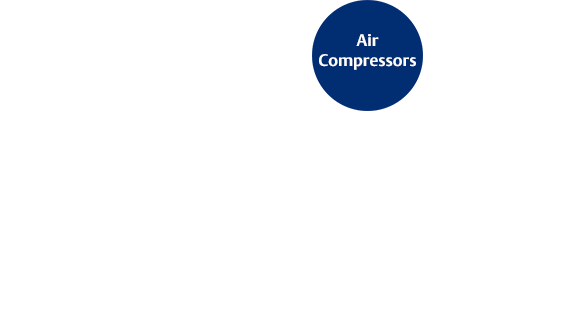
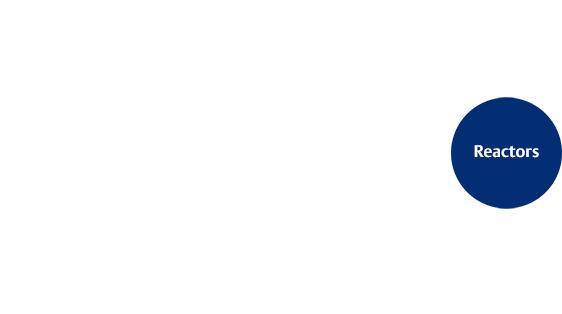
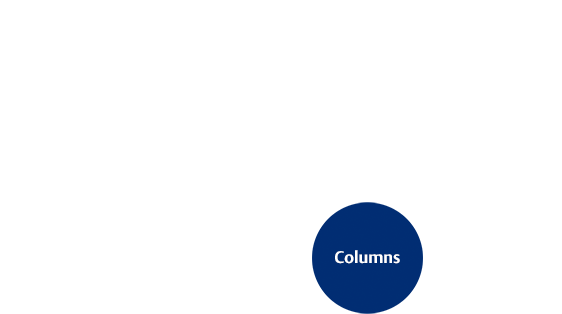
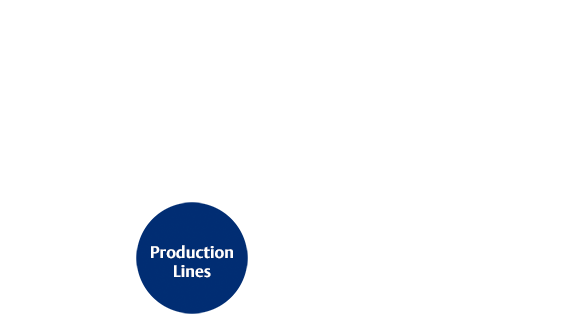
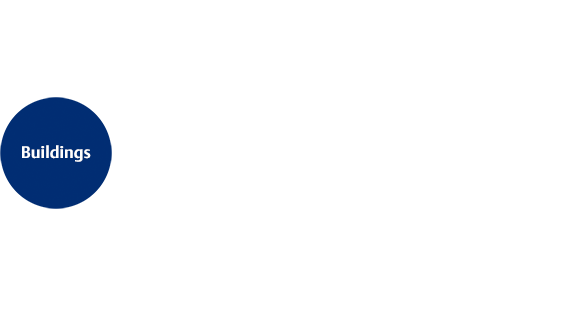
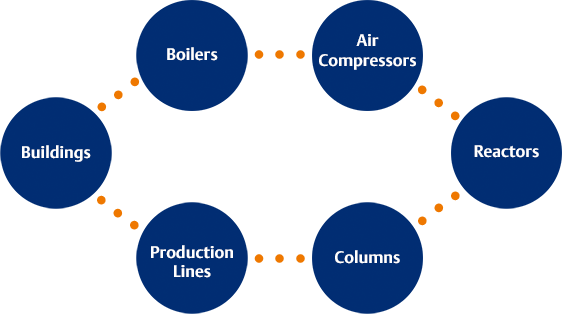
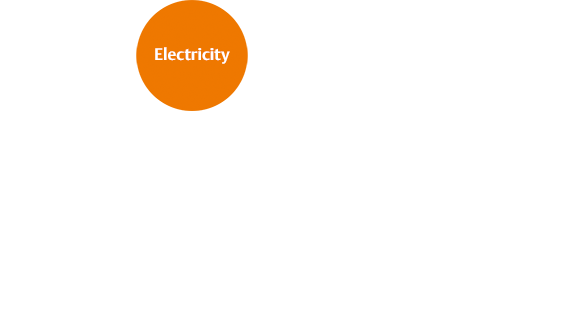
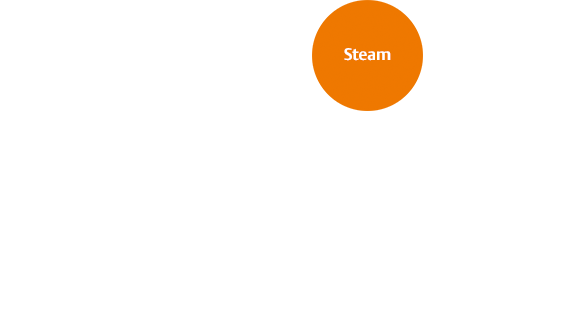
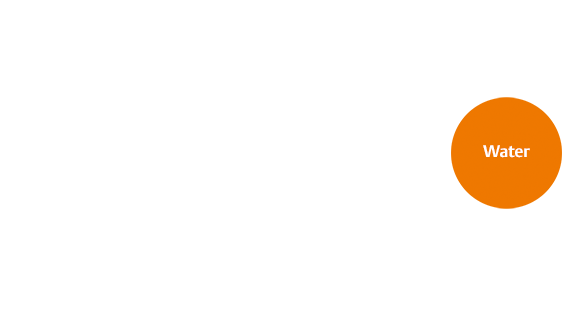
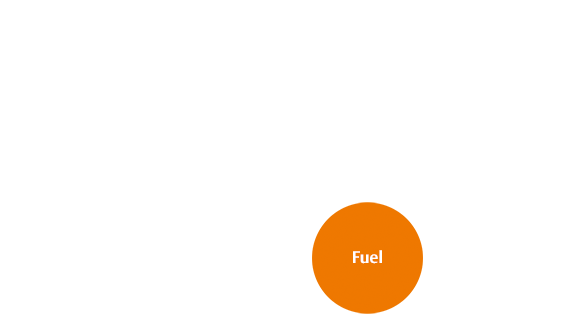
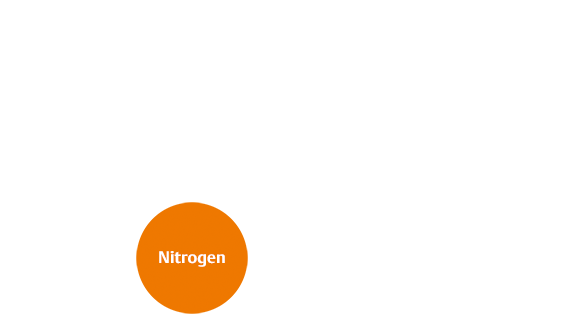

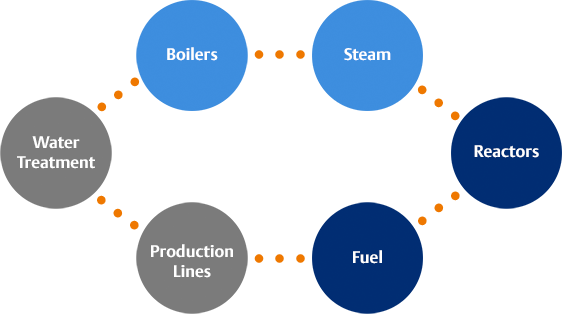
Energy Advisor includes five modules for managing energy productivity.
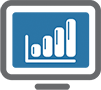
View energy
performance
and KPIs

Drive energy
saving
behavior
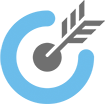
Create
Dynamic
Energy Targets
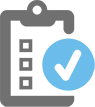
Create a
unique energy
hierarchy
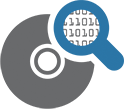
Verify
energy data
values
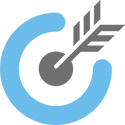
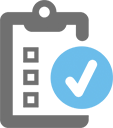
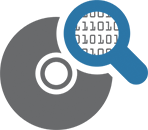
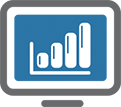
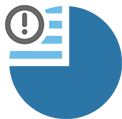
What Can I Expect?
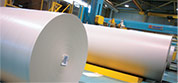
Bleach or Steam?
How a paper mill determined the cost efficiency between fuel and chemicals.

Minding the Capacitor Banks
Above-target consumption prompts a facility to check whether capacity banks can be switched off.
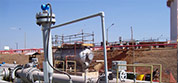
Taking a Cold Hard Look
A petrochemical facility in a northern climate is able to calculate the effect of cold temperatures on the product stream.
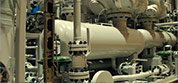
A Tale of Two Boilers
A paper mill discovers how to get twice as much steam from the same amount of natural gas.
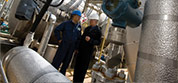
The Department of Redundancy Department
How many backup pumps does a facility really need?
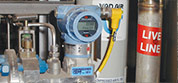
Not the Usual Suspect
An over-pressurized header costs a refinery thousands of dollars a day until Energy Advisor shows them the real cause of the problem.
What is the value of Energy Advisor in your plant?
The default values in the table below represent a real world case of Energy Advisor software combined with top down management
commitment to reduce waste and emissions. Replace the values with numbers from your plant to estimate the value to your plant.
Be advised total savings from an Energy Management Program are dependent upon a number of factors ranging from quality of measurements to management
commitment. Actual results may vary; the outcome from these calculations do not represent a commitment from Emerson Process Management.